The Evolution of the Roofing Industry
How Has the Roofing Industry Changed in the Last 30 Years?
Some things never change, right? Like roofing shingles. After all, they’re still made with asphalt and surfaced with granules just as they have been for many decades. Installers still overlap them and nail them to a wooden roof deck.
Like all businesses, the manufacture of asphalt roofing shingles evolves and changes over time. Companies introduce new roofing products to keep up with ever-changing roofing market trends. Evolutionary – and sometimes revolutionary – improvements are often made. This is certainly the case with asphalt shingles.
Let’s look at how some key trends in the roofing industry and changes in the manufacture of asphalt shingles over the past thirty years or so may inform your decisions in choosing the right shingle for your new roof.
Shingles and Roofing Technology Trends?
We usually associate the term “technology” with the computer or telecommunication industries but, over the last few decades, roofing shingle manufacturers have developed and adopted some pretty amazing technologies into their process.
In the “old days,” multi-layer laminated shingles had to be made offline, by hand. But in order to meet homeowners’ ever-growing demands, manufacturers had to engineer processes to produce laminated roofing products inline.
The result? Laminated shingles are now available in much more elaborate designs and high-definition profiles or shapes, all with enhanced color blends. You can even give your new roof the upscale look of natural slate tiles or genuine cedar shakes, without their worries or expense.
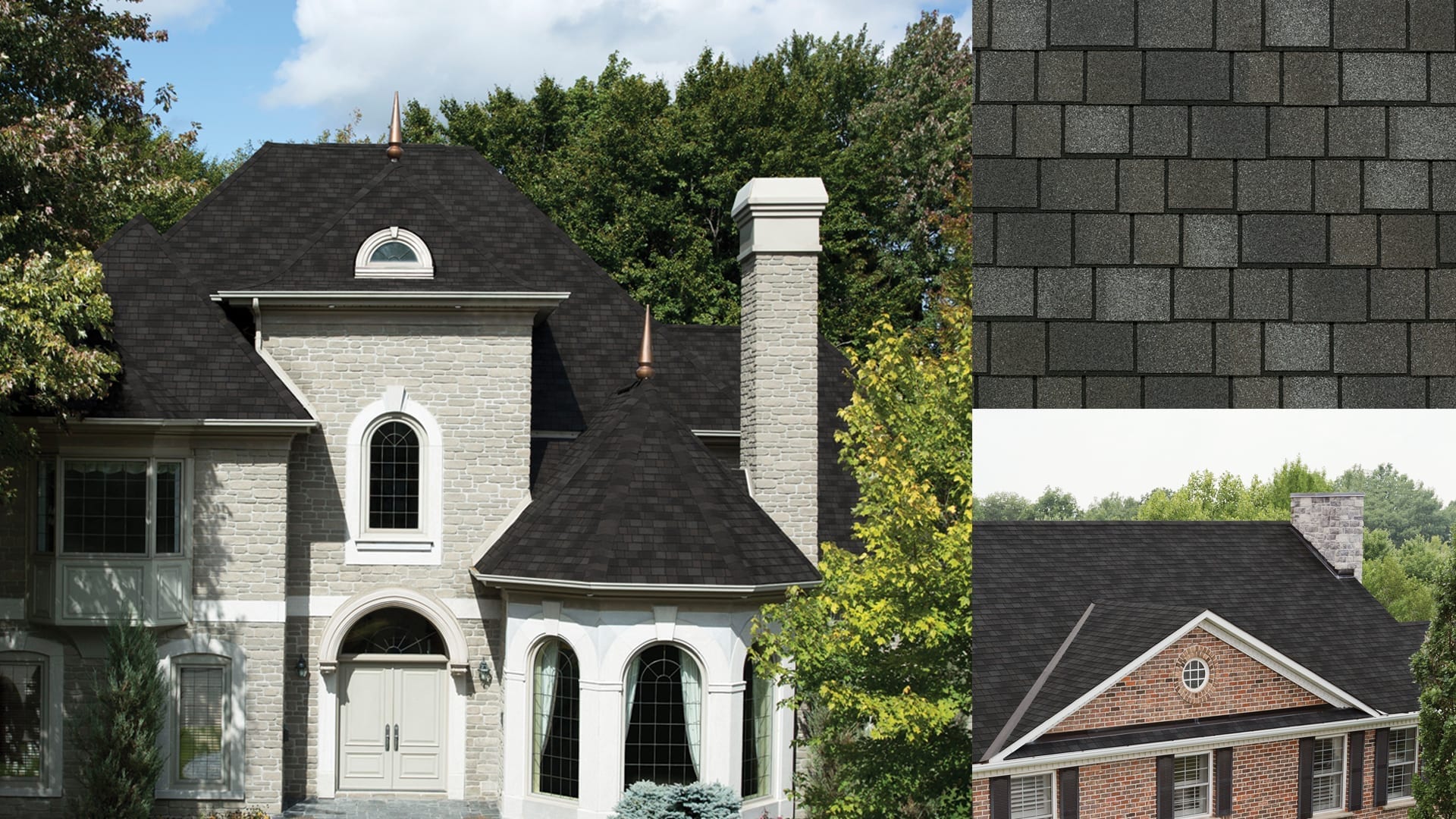
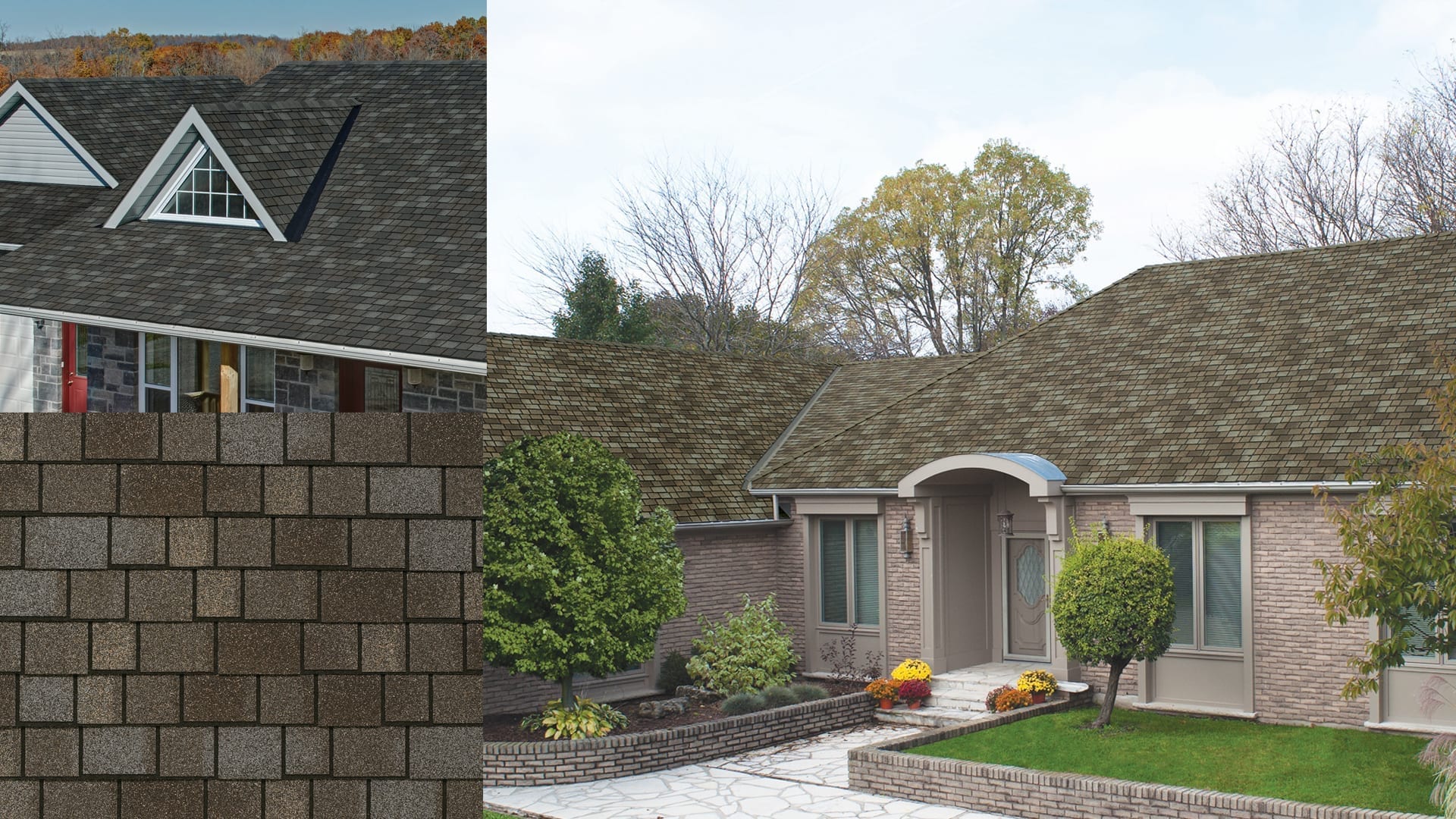
IKO Royal Estate shingles are an excellent example of how modern manufacturing techniques yield a sharper, higher-contrast laminated roofing shingle that mimics the appearance of natural slate tiles.
The introduction of computer-controlled systems in shingle manufacturing plants has greatly improved product uniformity in terms of raw material use, shingle weight, product dimensional control and appearance.
Thanks to similar controls on the granule application system, manufacturers can now make their shingle color blends not only more varied, but also more repeatable, resulting in greater consistency that helps reduce roof appearance issues.
All these improvements to the shingle manufacturing process have, over time, resulted in greatly increased speed and efficiency as well as better product at more affordable costs. It’s a big win/win for manufacturers and homeowners.
Out With the Old, In With The New
Asphalt shingles were originally manufactured on a base material made from cotton rags. Eventually, this rag base gave way to cellulosic reinforcements made with recycled paper, cardboard and wood fibers.
By the late 1970s and early 1980s, roofing shingles began to be made on fiberglass mat reinforcement. Interlocking shingle designs faded from the market in favor of the newer, easier-to-install laminated shingles.
At that time, manufacturers also introduced asphalt shingles with enhanced features such as granules containing algae-resistant additives. These specially designed granules were an important innovation as they helped inhibit the blue-green algae growth that can cause harmless, but unsightly, black streaks and stains.
Nowadays, most asphalt shingles are manufactured with these algae-resistant granules. Look for “AR” or the phrase “algae-resistant” on the brand you’re considering, if this is an important feature for a new roof in your area. Special UV stabilizers were also developed and added over the years to make the granules more color-fast to keep looking – and performing – great for longer.
In response to roofing installer demand, manufacturers developed laminated shingles with wider nailing zones. This made installation much faster and easier. It also made nail placement more accurate, to help resist wind blow-off better while at the same time requiring fewer nails to be used.
Some asphalt shingle manufacturers, including IKO, also started making their roofing shingles in a larger size. This not only speeds up installation, the larger exposure can also enhance a home’s curb appeal.
IKO Dynasty® asphalt shingles feature the “ArmourZone®” – a wider nailing area that creates a bigger, easier-to-hit target for installers. Shown the Glacier color blend.
Sometimes, innovations in asphalt shingle manufacturing have come about because of outside factors.
Today, many roofing shingles carry an independently tested impact-resistance rating, allowing homeowners to potentially receive a reduction in the cost of their home insurance policy. It’s important to understand that this is not a limited warranty of any kind; it’s strictly for the purposes of obtaining a discount on homeowner property insurance, where available. Ask your local agent for details.
Another external factor that has driven innovation in asphalt shingle manufacturing is the growing environmental consciousness. Homeowners’ concerns about energy costs and their carbon footprint have introduced legislation in some areas that affects the roofing industry.
Other Industry Advancements
Along with changes and advancements in asphalt shingle products and their manufacturing process, roofing accessories and related roofing materials have also improved. For example, ice dams have been a menacing phenomenon to roofs in northern regions for ages. Previously, added leak protection beneath the shingles at the eave area of a roof was provided by a messy mix of underlayment felts and asphalt cements.
But in the most recent generation, manufacturers have introduced self-adhering ice and water protector membranes that have made ice dam protection a simple, one-step process. These roofing products have subsequently also been adapted to create valley and roof penetration flashing to protect other critical roof areas.
At the peak of the roof, ridge capping used to be done by hand. Roofers would manually cut up shingle tabs, which was very time-consuming, labor-intensive and it wasted material. Specialty hip and ridge cap shingles have since evolved. These labor-saving accessory shingles are available to match and highlight the asphalt shingles in the field of the roof. Some are formed and shaped to provide a higher profile, adding further dimension and a dramatic appearance to the roofline. And, because cutting is no longer required, there are no scraps of excess material lying around so the roofers can keep the job site on your property neater and cleaner.

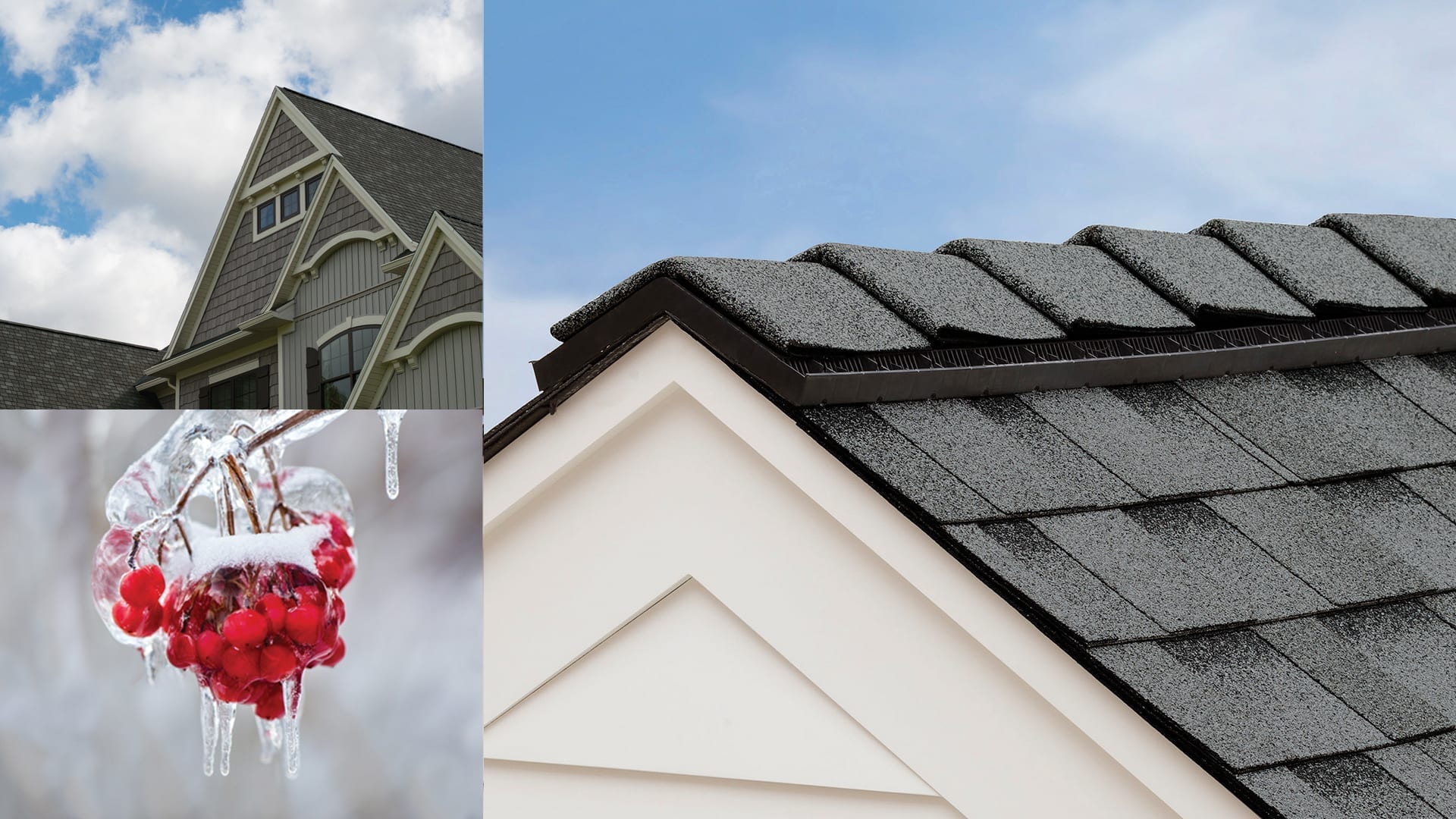
Specially constructed IKO UltraHP® ridge cap shingles are designed to provide a high-quality alternative to using cut-up roofing shingles to protect this important roof area.
Beneath the shingles there have been advancements as well. Traditional underlayments of asphalt-saturated felt are still available and widely used; however, synthetic underlayments have rapidly gained popularity since their introduction about fifteen years ago. Synthetic underlayments offer a variety of advantages including light weight, increased roll area and enhanced weather-resistance prior to shingle installation.
There’s one final small, but important, change to roofing shingles that you can see long before they’re installed. Thirty years ago, most asphalt shingles sold were wrapped in paper or cardboard when they arrived at the distributor’s yard or the homeowner’s job site. Unfortunately, if the package of shingles got wet or was exposed to the weather when stored outdoors, this wrapping was prone to disintegration. Now most roofing manufacturers wrap their shingle bundles in plastic film, which maintains its integrity much longer.
Installation
Installing shingles is tough work usually best left to professionals. The pros have added a few innovations of their own to make installation a little easier and more efficient. One of the more rigorous tasks in the “old days” was slogging the heavy shingle bundles up the ladder and onto the roof. These days, many roofers opt to have shingles delivered directly to the rooftop, to speed up the job and reduce the labor involved.
Experienced modern roofing contractors still have strong forearms, but much of that muscle now comes from manipulating nail guns. Most roofers agree that pneumatic tools, when used correctly and carefully, allow for faster and more efficient roof installation (although some of the old-school hand-nailing roofers feel just as passionately about using a good old-fashioned roofer’s hammer!). Raymond McNulty, Senior Consultant at IRC Building Sciences Group notes, “Having been in, or associated with the shingle industry since 1973, I have seen many changes that have contributed to advancements and improvements within the industry.”
“Among these changes, since the introduction of laminated shingles, their use has steadily grown to where they now dominate the market. In addition, the manufacturing process has improved to allow expanded production quantities at faster speeds than even fifteen or twenty years ago.” Although much has advanced in the asphalt shingle roofing industry, some fundamentals continue, such as the importance and value of proper attic ventilation and the need always to follow the shingle manufacturer’s installation instructions.
As the industry continues to grow and improve, asphalt shingles are very likely to continue to be the most frequently chosen roofing material in North America for the foreseeable future, thanks to their affordability and durability.
To find out more about the advantages of asphalt shingles and how to choose the right shingles for your home, visit our roofing shingles page to see the options and design possibilities.